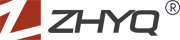
In industrial automation, pressure sensors play a vital role to make products intelligent and hyper-automated. Pressure sensors help people detect, analyze, measure and process various changes, such as changes in position, length, height, exterior and misalignment that occur in industrial production sites.
Industrial automation pressure sensors are input devices that provide an output (signal) regarding a specific physical quantity (input). Pressure sensors also play a pivotal role in predicting and preventing numerous potential processes, thus fulfilling the needs of many industrial sensing applications.
The following are several pressure sensors commonly used in automation:
1. Pressure sensor
A pressure sensor is an instrument that senses pressure and converts it into electricity, the amount of which depends on the applied pressure.
The main pressure sensors used in industrial automation include pressure sensors and vacuum pressure sensors. Pressure sensors are widely used in industrial and hydraulic systems, and these high-pressure industrial automation pressure sensors are also used in climate control systems.
Vacuum Pressure Sensor: Vacuum pressure sensors are used when the vacuum pressure is lower than atmospheric pressure and is difficult to detect by mechanical means. These pressure sensors typically rely on a heating filament whose resistance is temperature dependent. As vacuum pressure increases, convection decreases and wire temperature increases. The resistance increases proportionally and is calibrated near the pressure to allow for valid measurements of vacuum.
Pressure Applications of Pressure Sensors: Used to measure pressure below atmospheric pressure at a given location; used in meteorological instruments, aircraft, vehicles and other machinery that have implemented pressure capabilities; used in systems to measure other variables such as fluid/gas flow , speed, water level and height.
2. Temperature sensor
A temperature sensor is a device that collects information about temperature from a resource and changes it into a form that other devices can understand. It is a common category of pressure sensors that can detect temperature or heat and can measure the temperature of a medium.
The main temperature sensors used in automation include digital temperature sensors and temperature and humidity sensors.
Digital Temperature Sensor: A digital temperature sensor is a silicon-based temperature sensing C that provides accurate output by digitally representing the measured temperature. This simplifies control system design compared to approaches involving external signal conditioning and analog-to-digital converters (ADCs).
Temperature and humidity sensor: The temperature and humidity sensor combines a temperature sensor and a humidity sensor and then outputs a measured digital signal. By leveraging this technology and temperature and humidity sensing technology with limited digital signal acquisition, a high degree of consistency and excellent long-term stability is ensured.
Applications of temperature sensors: Continuous measurement of temperature in air, soil or water; for measurements in complex industrial applications; for measurements under harsh working conditions.
3.MEMS pressure sensor (microelectromechanical system)
MEMS industrial automation pressure sensors convert measured mechanical signals into electrical signals. Important pressure sensors used in industrial automation are acceleration and motion MEMS acceleration pressure sensors: Microelectromechanical systems (MEMS) acceleration pressure sensors are one of the main inertial pressure sensors. And with dynamic pressure sensor capabilities, it has a wider range of sensing capabilities.
Motion pressure sensor: Microelectromechanical systems (MEMS) motion pressure sensors use data processing algorithms designed on the motion interaction platform, which integrates many low-cost MEMS motion pressure sensors with ZigBee wireless technology to perform operations while working with machines. Personalized interactions. The pressure sensor signal processing system mainly solves problems such as noise elimination, signal smoothing, gravity-affected partitioning, coordinate system change and position information recovery. It is widely used in ABS technology in the automotive industry.
Applications of MEMS pressure sensors
MEMS pressure sensors are used in a wide range of applications, from industry, entertainment, sports to education. For example, triggering airbag deployment or monitoring nuclear reactors. As well as for measuring static acceleration (gravity), tilt of objects, dynamic acceleration in airplanes, vibrations to objects in cars, and vibrations of mobile phones, washing machines or computers. It is also used to detect motion and so on.
4. Proximity switch
The proximity switch is also designed and manufactured based on the principle of electromagnetic induction. Therefore, it can only detect metal targets, and the sensing distances of different metals vary slightly. Currently, the commonly used proximity switch detection distances are as follows: 1mm, 2mm, 4mm, 8mm, 12mm, etc.
There are usually two types of proximity switches: embedded type and non-embedded type. The so-called embedded type means that the sensor head of the proximity switch does not detect the metal target in the circumferential direction, but only detects the metal target in front of it, that is, the pressure sensor sensor head does not need to expose the metal mounting bracket; the so-called non-embedded type means that the proximity switch senses The head not only detects the metal target in front of it but also detects the metal target in the circumferential direction. That is, the pressure sensor sensing head must expose the metal mounting bracket for a certain distance and there must be no metal targets within a certain range in the circumferential direction to avoid misjudgment.
The detection accuracy of proximity switches is higher than that of magnetic switches. Proximity switches are usually used to determine whether the product is present and whether the tooling fixture is in place, etc. where the position accuracy is relatively low.
5. Displacement sensor
As the name suggests, it is a sensor that detects changes in the position of a target object. The displacement sensor is also called a linear sensor. It is a linear device that belongs to metal induction. The function of the sensor is to convert various measured physical quantities into electricity.
In the production process, the measurement of displacement is generally divided into two types: physical size measurement and mechanical displacement. According to the different forms of transformation of the measured variable, displacement sensors can be divided into two types: analog and digital.
Analog type can be divided into two types: physical type and structural type. Commonly used displacement sensors are mostly of analog structure type, including potentiometer displacement sensors, inductive displacement sensors, self-aligning machines, capacitive displacement sensors, eddy current displacement sensors, Hall displacement sensors, etc.
An important advantage of digital displacement sensors is the ease of sending signals directly into the computer system. This kind of pressure sensor develops rapidly and is used increasingly widely.
6. Intelligent pressure sensor
The last type of pressure sensor may also be the most important one in the future automation industry – smart pressure sensor.
A new generation of advanced intelligent pressure sensors will become the heart of industrial automation. “Smart factory” refers to the use of Internet of Things technology and equipment monitoring technology to strengthen information management and services based on the digital factory, clearly grasp the production and marketing process, improve the controllability of the production process, reduce manual intervention on the production line, and ensure timely and correct Collect production line data locally, as well as reasonable production plan arrangement and production progress. Technologies that can be implemented in smart factories include wireless sensing, control system networking, and wireless industrial communications, such as weighing and pressure sensors.
Quickly and directly measure and control certain product quality indicators (such as viscosity, hardness, surface finish, composition, color and taste, etc.) online. Pressure sensors integrating intelligent technology will be able to solve the above problems very well.
Your email address will not be published. Required fields are marked *