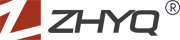
Real-time monitoring, precise control! Shanghai Zhaohui inline refractometer protects the lifeline of chemical safety and efficiency!
In the complex and ever-changing chemical production process, material concentration is a core parameter that affects the entire system:
-Is the raw material ratio in the reactor accurate, which directly determines the conversion rate and product purity?
-At the key nodes of evaporation, crystallization, and extraction, does the concentration meet the standard, affecting the yield and energy consumption?
-In acid-base neutralization and solution preparation, does the concentration deviation lead to quality fluctuations or even safety accidents?
-Are the concentrations of expensive catalysts and additives within the optimal range to avoid waste?
Traditional offline testing that relies on manual sampling and laboratory analysis is inefficient in modern chemical production:
-Severe lag: When the results come out, the entire batch of materials may have deviated from the process window, which may lead to quality degradation or safety risks.
-Lack of representativeness: Intermittent sampling makes it difficult to capture transient changes in concentration in continuous flow or dynamic reactions.
-Inefficiency: It consumes manpower, affects production rhythm, and increases operational risks (especially when dangerous goods are involved).
-Data islands: It is difficult to integrate into the DCS/PLC system in real time to achieve automated closed-loop control.
How to break through the bottleneck of concentration monitoring and achieve safer, more efficient and leaner chemical production?
Shanghai Zhaohui inline refractometer: “real-time concentration monitoring guard” of chemical process:
Shanghai Zhaohui Pressure Instrument Co., Ltd., as a reliable partner in the field of industrial process measurement, provides high-performance, high-reliability and high-adaptability inline refractometer series products (including online refractometer, online density meter, etc.) with deep technical accumulation. We install “never tired process eyes” for your pipelines, reactors and storage tanks to continuously, real-time and accurately monitor the concentration of key materials 24 hours a day, 7 days a week, enabling intelligent production and safe operation!
Core values: safety, stability, and efficiency, driving excellent chemical operations!
1. Real-time and accurate monitoring to build a solid safety line:
–Instant warning: Set concentration safety thresholds (such as excessive reactants, unqualified products, and formation of dangerous mixtures). Once exceeded, immediately trigger an audible and visual alarm or interlock the DCS system through a relay/communication interface to automatically execute safety measures (such as cutting off feed, emergency discharge), effectively preventing safety accidents such as material leakage, explosion, and unqualified products.
–Ensure compliance: Accurately monitor the concentration of key components in environmental treatment fluids (such as desulfurization and denitrification fluids, wastewater treatment agents) to ensure that emissions meet standards and avoid environmental risks.
2. Optimize process control to improve product quality and yield:
–Reaction process control: Real-time monitoring of reactant/product concentration changes, accurate control of feed ratio, judgment of reaction endpoint, maximization of conversion rate and selectivity, and improvement of product purity and consistency.
–Separation process optimization: Real-time tracking of concentration changes in unit operations such as evaporation, crystallization, distillation, and extraction:
. Accurately judge the evaporation/concentration endpoint to avoid over-concentration and waste of energy or product deterioration, and significantly reduce steam consumption.
. Control crystallization supersaturation, optimize crystal growth, and improve product particle size and yield.
. Guide the adjustment of extractant ratio to improve separation efficiency.
–Precise batching and mixing: Real-time monitoring of solution concentration in mixing tanks or pipelines to achieve closed-loop automatic adjustment to ensure accurate formula.
3. Reduce operating costs and tap into the potential for benefits:
–Reduce raw material waste: Avoid over-feeding, defective products, rework, or even whole batch scrapping due to uncontrolled concentration, saving expensive raw materials (catalysts, specialty chemicals, etc.).
–Reduce energy consumption: By optimizing processes such as evaporation and drying (precisely controlling the end point), steam and electricity consumption can be significantly reduced.
–Improve equipment efficiency: Stable and optimized process conditions reduce equipment abnormal fluctuations and scaling, and extend equipment operation cycle and life.
–Save labor costs: Completely replace frequent and dangerous manual sampling and laboratory analysis, free up manpower, and improve efficiency.
4. Meet the tough challenges and operate stably and reliably:
–The King of Corrosion Resistance: Provide a full range of corrosion-resistant material probes/sensors, including but not limited to:
. Stainless steel 316L
. Hastelloy (C276, C22)
. Titanium alloy (Ti, Gr2)
. Zirconium (Zr702)
. Tantalum (Ta)
. PTFE/ PFA full wrap option (for highly corrosive, high viscosity, and easy-to-adhere media)
— Rugged and durable: High protection level (IP66/IP67/IP68/IP69K), adaptable to the humid, dusty, and flushing environment of chemical sites.
— Explosion-proof certification: Key models have passed international explosion-proof certifications such as ATEX and IECEx, meeting the safety requirements of hazardous areas such as Zone 1/Zone 2.
— Wide adaptability to temperature and pressure: Customizable high temperature resistant (up to 90°C+) and high pressure resistant (up to several hundred Bar) versions, adaptable to working conditions such as reactors and high-pressure pipelines.
–Anti-pollution design: For viscous, solid-containing, easy-to-crystallize, and easy-to-scale media:
. Optional ultrasonic self-cleaning function to keep the measuring surface clean.
. Specially designed flow channel/scraper (densitometer).
. Flushing interface design.
–Intelligent temperature compensation: High-precision temperature sensor and algorithm to ensure accurate measurement in a wide temperature range.
Widely used scenarios:
1. Basic chemicals: acid/base concentration monitoring (H2SO4, HCl, NaOH, KOH, etc.), brine concentration, hydrogen peroxide concentration, reactant ratio control.
2. Petrochemicals: catalyst concentration, solvent concentration, alkylation acid concentration, amine solution concentration (desulfurization and decarbonization), oil blending.
3. Fine chemicals/pharmaceutical intermediates: synthesis reaction monitoring, crystallization process control, extract concentration, solvent recovery concentration, intermediate/API concentration.
4. Pesticides/fertilizers: mother liquor concentration, reaction endpoint judgment, fertilizer solution concentration control.
5. Environmental protection/water treatment: desulfurization and denitrification absorption liquid concentration, wastewater treatment agent concentration (PAC, PAM, acid and alkali, etc.), circulating cooling water concentration multiples.
6. Daily chemicals/paints: emulsion concentration, resin solution concentration, pigment slurry solid content/concentration.
7. New energy materials: electrolyte concentration, precursor solution concentration.
ZHAQ’s advantages: your professional chemical measurement partner
1. In-depth industry understanding: We deeply understand the complexity of chemical processes and the stringent requirements for measurement.
2. Rich product lines: We provide inline refractometers based on various principles such as refraction, density, and sound velocity, and recommend the best solution based on specific media and working conditions.
3. Highly customized: We provide flexible customization in terms of materials, process connections, pressure/temperature resistance grades, explosion-proof certification, signal output, etc.
4. Professional technical support: We have an experienced team of chemical application engineers, providing a full range of services from selection consultation, solution design, installation guidance to commissioning and maintenance.
5. Reliable quality and supply chain: Strict quality control system to ensure long-term and stable operation of products.
6.Localized rapid response: Timely and efficient pre-sales and after-sales services to ensure your worry-free production.