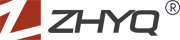
There are a ubiquitous number of pressure transducer designs available for use in any number of industrial or laboratory applications. These include the industrial pressure transducer, the liquid pressure transducer, and the micro pressure transducer, among others.
Pressure transducers can come in a number of shapes and sizes, but the majority of transducers have a cylinder-shaped center which houses the diaphragm and the measurement pressure chamber, a pressure port at one end which is typically a threaded, bolted, barbed fitted, or open, and on the other end a location for signal transmission.
Designs in pressure transducers
Each pressure transducer has different aspects that will impact how it works and the applications the pressure transducer works best for. Here are the most common types of pressure transducers:
Low Cost Compact Pressure Transmitter
Pressure transmitters with compact, rugged, and stainless-steel body that are designed to integrate with a variety of industrial and OEM applications.
PC Board Mountable Pressure Transducers
Designed to mount on an electrical PC board and be integrated into other products, PC board mountable pressure transducers are generally compact and economical.
General Purpose Transducers
General purpose pressure transducers are the most common since they are designed to fit the broadest set of applications.
Heavy Duty/Industrial Pressure Transducers
Heavy duty/Industrial pressure transducers feature a much more rugged enclosure than other transducers. They are designed to accommodate heavy industrial environments. They also often feature a scalable 4-20mA output that provides much greater immunity to electrical noise, which is not uncommon in industrial environments.
High Stability/High Accuracy Pressure Transducers
Most pressure transducers feature an accuracy of 0.25% of full scale or higher. High stability and high accuracy pressure transducers can offer errors as low as 0.05% of full scale, depending on model. Although more expensive than general purpose transducers, they may be the only option if high precision is required. These include pressure transducers such as a high pressure pressure transducer, low pressure pressure transducer, barometric pressure transducer, liquid pressure transducer, and a digital pressure transducer.
Flush Diaphragm Pressure Transducers
With flush diaphragm pressure transducers, the diaphragm is flush to the process. This eliminates a cavity above the diaphragm that could collect fluid matter from the process. In certain applications, this may be very undesirable. Those applications include monitoring the pressure of foods or liquids that have very high viscosity.
Special Purpose Transducers
ZHYQ offers a variety of pressure transducers with special features. These include pressure transducers designed for pressure measurement in very high or low temperatures, submersible pressure transducers, barometric pressure transducers, and pressure transducers with digital communications output or wireless outputs.
Technologies in pressure transducers
Here are brief descriptions of the different types of pressure transducers available, including the operating principles and pros and cons of each.
Strain Gauge
Strain gauge-type pressure transducers are widely used, especially for narrow-span pressure and for differential pressure measurements. These devices can detect gauge pressure if the low pressure port is left open to the atmosphere or differential pressure if connected to two process pressures. If the low pressure side is a sealed vacuum reference, the transmitter will act as an absolute pressure transmitter.
Strain gauge transducers are available for pressure ranges as low as 3 inches of water to as high as 200,000 psig (1400 MPa). Inaccuracy ranges from 0.1% of span to 0.25% of full scale. Additional error sources can be a 0.25% of full scale drift over six months and a 0.25% full scale temperature effect per 1000¡ F.
Capacitance Pressure Transducers
Capacitance pressure transducers were originally developed for use in low vacuum research. Capacitance change results from the movement of a diaphragm element. Depending on the type of pressure, the capacitive transducer can be either an absolute, gauge, or differential pressure transducer.
Capacitance pressure transducers are widespread in part because of their wide rangeability, from high vacuums in the micron range to 10,000 psig (70 MPa). Differential pressures as low as 0.01 inches of water can readily be measured. And, compared with strain gage transducers, they do not drift much. Better designs are available that are accurate to within 0.1% of reading or 0.01% of full scale. A typical temperature effect is 0.25% of full scale per 1000¡ F.
Capacitance-type sensors are often used as secondary standards, especially in low-differential and low-absolute pressure applications. They also are quite responsive, because the distance the diaphragm must physically travel is only a few microns. Newer capacitance pressure transducers are more resistant to corrosion and are less sensitive to stray capacitance and vibration effects that used to cause “reading jitters” in older designs.
Stainless steel is the most common diaphragm material used, but for corrosive service, high-nickel steel alloys, such as Inconel or Hastelloy, give better performance. Tantalum also is used for highly corrosive, high temperature applications. As a special case, silver diaphragms can be used to measure the pressure of chlorine, fluorine, and other halogens in their elemental state.
Potentiometric Pressure Transducers
The potentiometric pressure sensor provides a simple method for obtaining an electronic output from a mechanical pressure gauge. The device consists of a precision potentiometer, whose wiper arm is mechanically linked to a Bourdon or bellows element. The movement of the wiper arm across the potentiometer converts the mechanically detected sensor deflection into a resistance measurement, using a Wheatstone bridge circuit.
The mechanical nature of the linkages connecting the wiper arm to the Bourdon tube, bellows, or diaphragm element introduces unavoidable errors into this type of measurement. Temperature effects cause additional errors because of the differences in thermal expansion coefficients of the metallic components of the system. Errors also will develop due to mechanical wear of the components and of the contacts.
Potentiometric transducers can be made extremely small and installed in very tight quarters, such as inside the housing of a 4.5-in. dial pressure gauge. They also provide a strong output that can be read without additional amplification. This permits them to be used in low power applications. They are also inexpensive. Potentiometric transducers can detect pressures between 5 and 10,000 psig (35 KPa to 70 MPa). Their accuracy is between 0.5% and 1% of full scale, not including drift and the effects of temperature.
Resonant Wire Pressure Transducers
The resonant-wire pressure transducer was introduced in the late 1970s. In this design, a wire is gripped by a static member at one end, and by the sensing diaphragm at the other. An oscillator circuit causes the wire to oscillate at its resonant frequency. A change in process pressure changes the wire tension, which in turn changes the resonant frequency of the wire. A digital counter circuit detects the shift. Because this change in frequency can be detected quite precisely, this type of transducer can be used for low differential pressure applications as well as to detect absolute and gauge pressures.
The most significant advantage of the resonant wire pressure transducer is that it generates an inherently digital signal, and therefore can be sent directly to a stable crystal clock in a microprocessor. Limitations include sensitivity to temperature variation, a nonlinear output signal, and some sensitivity to shock and vibration. These limitations typically are minimized by using a microprocessor to compensate for nonlinearities as well as ambient and process temperature variations.
Resonant wire transducers can detect absolute pressures from 10 mm Hg, differential pressures up to 750 in. water, and gauge pressures up to 6,000 psig (42 MPa). Typical accuracy is 0.1% of calibrated span, with six-month drift of 0.1% and a temperature effect of 0.2% per 1000¡ F. .
Your email address will not be published. Required fields are marked *