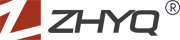
Corrugated market – fast growing driven by eCommerce:
Corrugated Board Industry is fast growing at a CAGR of more than 4% with volumes of more than 115 million tons valued in excess of $176 billion in 2019.
Packaging made from corrugated board is considered environmentally friendly and sustainable. It contains only natural raw materials (wood pulp, starch glue, and 80% recycled paper) and is therefore 100 percent renewable, recyclable and biodegradable. Even the process of processing and printing corrugated board is environmentally friendly because the inks are mainly water-based.
There are many types of boxes made by the corrugating industry, ranging from lightweight micro-flute up to heavy-duty multi-wall boxes. Low-cost, high-performance cardboard boxes are a versatile means of packing many different types of products, including machinery, electrical goods, fruit and vegetables, as well as a means of providing information and advertising about the contents.
Corrugated boxes must meet multiple demands, but it all starts with the production of a strong, flat board on the corrugator.
As important as the choice of papers is, the adhesive and its application are crucial to getting the best corrugated board at the end of the corrugating machine. To be effective on a wide variety of boards, glues must be versatile while maintaining quality bonding and high productivity. Adhesion between the liners and medium must be strong to provide strength and cushioning to protect the contents from the outside world and allow the box to maintain integrity through its life cycle.
All starch adhesives are based on a special property of starch: when subject to heat, starch slurry undergoes an extremely rapid increase in viscosity as the starch granules gel. This high viscosity, developed at a critical temperature, leads to the phenomenon of tack.
As the correct viscosity is crucial to the proper functioning of the starch, viscosity control can help improve the consistency and performance of these adhesives in many corrugated cardboard products.
What is the need for process control in corrugated board production?
Following paper production, corrugated board is the second largest application of non-food starches globally, where it is used as an adhesive between the fluting and liners. Many starch glues contain unmodified native starch, along with additives such as borax and caustic soda. Gelatinized starch carries uncooked starch slurry and prevents sedimentation. Such a glue is called an opaque SteinHall adhesive.
The glue is applied on the medium flute tips, after which the other paper component known as the liner is brought into contact and bonded. This is then dried under high heat, which causes the rest of the uncooked starch in the glue to swell/gelatinize. This gelatinization provides the final setting reaction making the glue a fast and strong adhesive for corrugated board production.
The quality and integrity of the product inside the box relies on the stability of the packaging. And a box’s ability to protect the contents inside often depends on the strength and proper application of the adhesive.
Starch application viscosity control solutions help to ensure that each batch of adhesive has the right consistency and that it is applied in the right quantities and positions during the gluing of the flutes to the liners. An inline viscometer is used to optimize and consistently maintain the correct starch thickness for the adhesive layer.
Importance of viscosity and density monitoring and control to ensure high quality starch adhesion
Corrugated paperboard production depends highly on adhesion, which has the greatest impact on its quality. It is the quality of starch glue that ultimately determines the quality of adhesion. Viscosity is an important metric of starch glue, and the amount of viscosity directly affects the adhesion of corrugated boards. Stable viscosity is the only way to ensure good adhesion properties of starch glue.
Components and production of starch adhesives
When the viscosity of starch/adhesive is outside the optimal range, it creates imperfections and reduces the quality of the intermediate and end products. An adhesive with sufficient viscosity will prevent blankets and papers from being impregnated, thereby improving their quality.
Most recipes for starch glue for corrugated plants consist of:
These ingredients are mixed and heated to achieve a target viscosity. Factors affecting starch viscosity are type and quality of starch, oxidant dosage and oxidation time, oxidation temperature, dosage of gelatinizer NaOH (Sodium Hydrooxide), borax dosage, water ratio and storage temperature, time and environment. With so many parameters and constituents to get right during starch production/formulation, it pays back quickly to monitor the end-product (starch) to ensure batch consistency.
Viscosity is an important indicator of the particle size distribution. Changes in the particle size distribution can affect properties such as density, rheology and layer thickness. Properties related to particle size distribution in starch are, for example, the flexibility, strength and usability of the (corrugated) cardboard.
The starch glue belongs to the polymer product family. There are two types of glucose polymers in starch: linear and helical amylose and branched amylopectin. Depending on the plant, starch contains 20% to 25% amylose and 75% to 80% amylopectin. Since amylose fractions aren’t truly soluble in water, they eventually form crystalline aggregates by hydrogen bonding – a process called retrogradation or setback, which makes viscosity unstable. It exhibits complex rheological behavior. Inline viscosity monitoring can catch when the starch formulation has gone bad or is non-optimal for application.
Why automate incoming material inspection and application of adhesives, glues, paste and hot melts?
There are many different types of adhesives, including viscous liquids, paste, crystalline and amorphous solids. Furthermore, adhesives are typically packaged in cartridges, pails, drums, totes, pellets, and blocks. It is critical for a production process to have a steady flow of adhesive from the adhesive container into the dispensing equipment to keep it running continuously. Hot melt adhesives are solids at room temperature, so they are usually removed manually from boxes by scooping and then added to melting equipment to be dispersed during the melting process.
If not carefully monitored, manual handling creates additional tasks for operators, runs the risk of contamination during handling, and leaves open the possibility of spills or even process downtime. A steady consumption of hot melts also minimizes the heat history of the adhesive, which enables maximum performance and quality in the production process.
Benefits of viscosity automation in corrugating process
Solutions that automate adhesive delivery are gaining popularity as more manufacturers realize the benefits and quick ROI, including:
Your email address will not be published. Required fields are marked *